Understanding the Order Processing Pipeline
Mastering e-commerce order processing requires a comprehensive grasp of the entire workflow, starting when an order is placed until it reaches the customer's doorstep. Recognizing each phase, pinpointing possible slowdowns, and understanding how these stages interconnect are vital for operational success. An effective system must manage all steps flawlessly to guarantee satisfaction for both shoppers and businesses alike.
Meticulous documentation of every action helps uncover inefficiencies. This information enables teams to spot problems early and implement solutions quickly, ensuring orders move through the system accurately and on schedule. Additionally, establishing straightforward communication channels between departments is crucial for meeting delivery deadlines.
Optimizing Order Entry and Validation
Perfecting the order entry process is critical. An intuitive interface paired with rigorous validation protocols dramatically decreases mistakes while guaranteeing precise order details from the beginning. Automated verification systems can identify discrepancies early, preventing expensive errors later. These systems should confirm customer details, product stock levels, and shipping choices to reduce delays and enhance shopper satisfaction.
Top-tier order entry platforms need direct connections with inventory databases, providing live updates on product availability. This forward-thinking method removes the possibility of accepting orders for unavailable merchandise, preserving customer trust and brand reputation.
Improving Inventory Management
Precise stock control forms the backbone of efficient order processing. Live inventory monitoring helps businesses prevent overselling while ensuring timely order completion. A system that instantly adjusts stock quantities after each transaction is indispensable for maintaining precision and avoiding shortages. This technology should integrate with the order management platform to provide accurate data throughout the entire fulfillment sequence.
Enhancing Order Fulfillment Processes
Superior order fulfillment is fundamental to smooth operations. This involves refining warehouse activities, simplifying product retrieval, packaging, and dispatch procedures, plus ensuring correct labeling and tracking details. Introducing automation for repetitive jobs can slash error rates while boosting productivity.
Creating a mechanism to rank orders by urgency and customer value further improves fulfillment. Combined with transparent status updates for customers, this approach delivers a reliable and satisfying purchasing journey.
Leveraging Technology for Automation
Modern tools are transforming order processing efficiency. Automated solutions can manage routine tasks, cutting down on manual work and reducing mistakes. These include processing orders automatically, creating shipping documents, and communicating with customers. By implementing these technologies, companies can redirect valuable resources to other critical business areas.
Connecting different software platforms - like order management, warehouse systems, and customer databases - enables seamless information sharing and instant updates across all operations. This holistic technological integration dramatically enhances accuracy and productivity.
Implementing Effective Communication Strategies
Clear communication during the order journey is essential for building customer confidence. Establishing reliable channels for order updates, shipping notifications, and delay alerts is crucial. This means quickly informing customers about any changes and providing shipment tracking options.
Forward-looking notifications, like pre-delivery alerts, elevate the customer experience. Keeping shoppers informed helps them prepare for arrivals while reinforcing positive brand relationships throughout the purchasing process.
Measuring and Monitoring Performance
Tracking key performance metrics is vital for assessing order processing effectiveness. Important measurements include fulfillment speed, order precision, customer satisfaction levels, and delivery times. Regular analysis of these indicators highlights improvement opportunities and supports ongoing process refinement.
Using data analysis to spot patterns in order handling enables proactive adjustments. This continuous evaluation is critical for identifying workflow obstacles and optimizing the entire order management system.
Inventory Management: The Foundation of Efficient Fulfillment
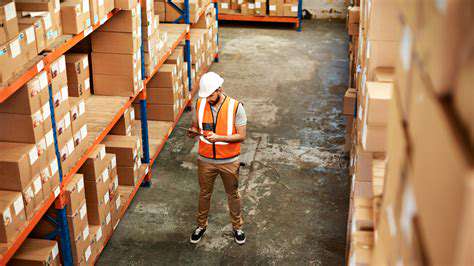
Inventory Management Strategies
Smart inventory approaches benefit businesses regardless of size. These methods extend beyond basic stock tracking to include demand prediction, storage optimization, and timely restocking. Sophisticated inventory systems are indispensable for reducing storage expenses while boosting earnings. By examining past sales, market movements, and production capabilities, companies can create precise forecasting models to meet future requirements while avoiding shortages or excess inventory.
Demand Forecasting and Planning
Precise demand prediction anchors successful inventory control. Understanding buying behaviors, seasonal variations, and market shifts is essential for anticipating needs. Accurate forecasts let businesses adjust stock proactively, ensuring product availability while minimizing missed sales opportunities. Advanced software and analytical techniques can significantly improve prediction accuracy.
Inventory Control Systems
Deploying a robust inventory tracking system is crucial for operational efficiency. The ideal system monitors stock levels continuously, allowing businesses to watch inventory, spot potential deficits, and initiate automatic reorders. A well-designed control system offers complete visibility of available products, supporting data-driven decisions and proactive inventory oversight. Features should include barcode scanning, automated purchasing, and live tracking capabilities.
Warehouse Management
Effective warehouse operations are integral to inventory success. Optimizing space usage, improving layout design, and implementing proper storage protocols help minimize costs while preserving product quality. Proper warehouse practices decrease damage risks and product obsolescence, enhancing overall operational effectiveness. This often involves strategic placement of popular items for quick access and implementing clear identification methods.
Cost Optimization Strategies
Reducing inventory expenses is a primary objective for any business. This requires careful evaluation of purchasing costs, storage fees, and shortage penalties to find improvement opportunities. Implementing cost-saving measures increases profits while improving financial flexibility. Effective tactics include negotiating better supplier terms, optimizing order quantities, and employing efficient storage solutions.
Risk Management and Mitigation
Comprehensive inventory planning includes anticipating and addressing potential threats. This means considering supply chain interruptions, demand fluctuations, and possible product phase-outs. Creating backup plans for emergencies like supplier failures or natural disasters ensures uninterrupted operations. Strong risk management safeguards against losses while maintaining business stability.
Inventory Turnover and Cycle Time
Analyzing inventory turnover and processing duration offers valuable performance insights. Higher turnover rates typically indicate effective management, streamlined ordering, and accurate demand prediction. Boosting turnover reduces storage expenses and releases funds for other business requirements. Examining the complete inventory cycle - from receipt to sale - reveals opportunities for process enhancements.
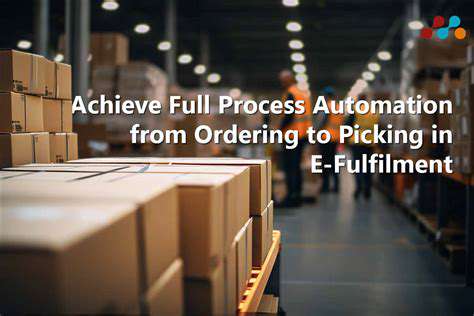
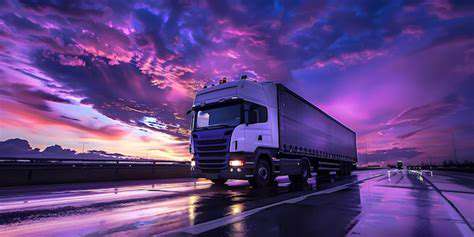